Dyed rope & dyeing rope yourself
Colorful ropes are become more and more popular. Being it either for pure aesthetics or just because you like a color. When using dyed rope, you should consider a few factors. When dyeing rope yourself, you should be very careful and follow our best practices to make the best out of your rope.
1. Buying dyed rope
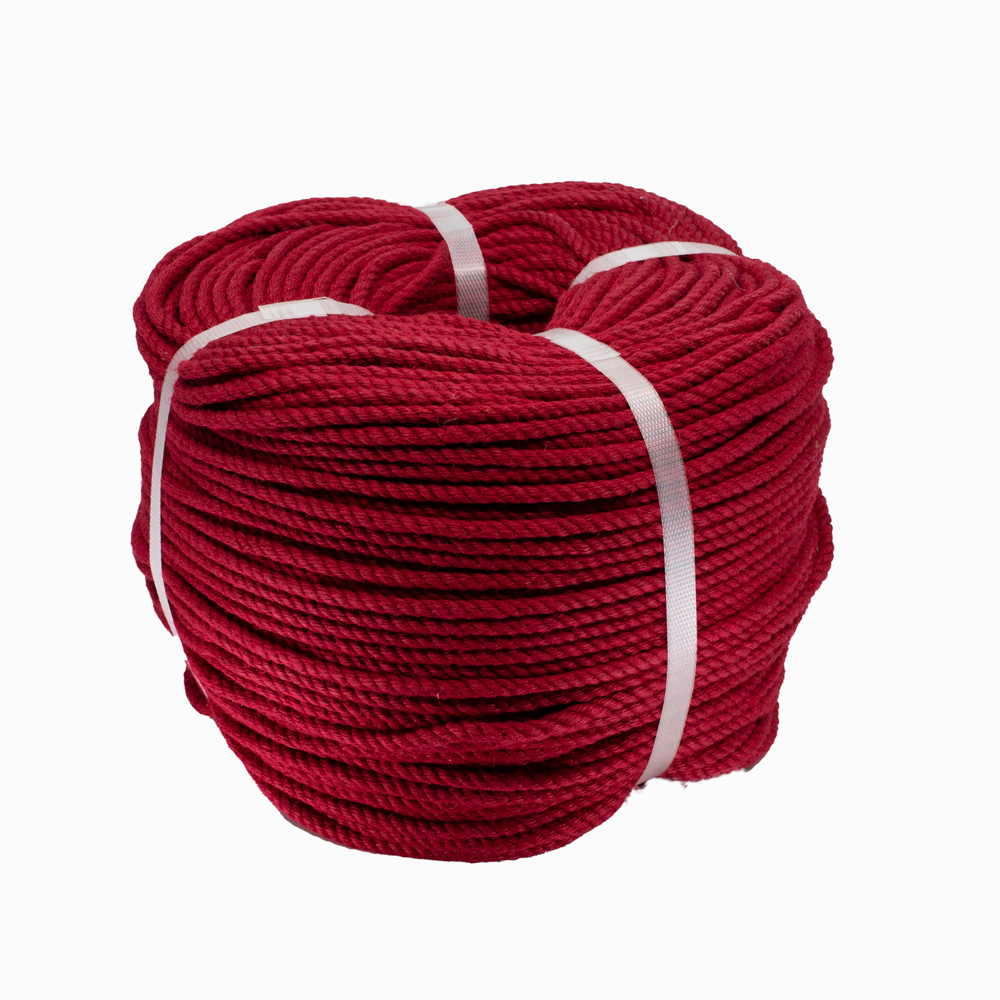
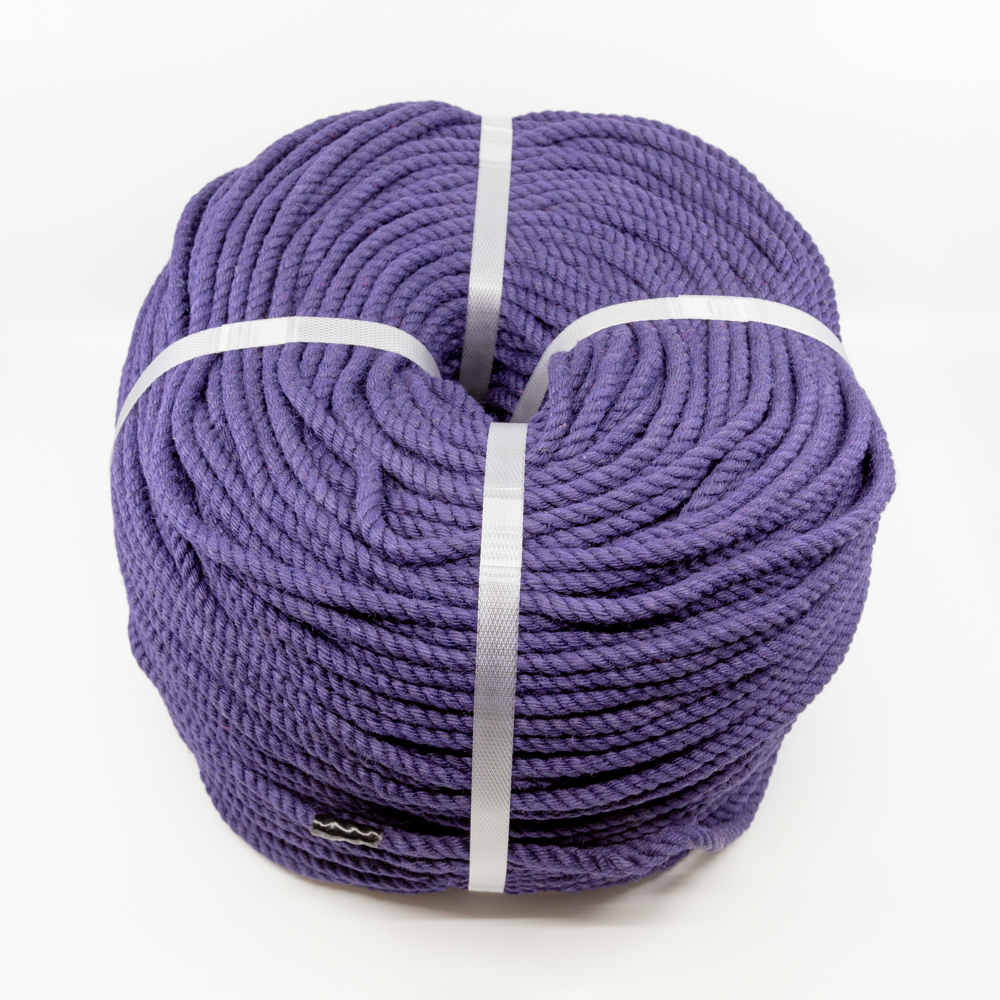
The best way to get beautiful colored rope is to dye the yarn before rope productions. However this requires large, industrial machines to dye hundreds of meters of ropes. When dyeing ropes in such machines, the process needs to be very well engineered and controlled to produce good quality rope. Therefore most of the rope you can buy today is cut to length and dyed afterwards.
Machine or manual dyeing
A big question on both quality and price are whether the rope has been dyed in a machine (e.g. washing machine) or by hand. Dyeing in a machine is less effort and ensures a more consistent color across the rope. Manual dyeing, e.g. by hand, gives a better control over the process, such as temperature, length of dyeing process and so on. Hence, you should ask, which method is used for dyeing and how rope parameters such as strength, diaemeter and tension are ensured.
Conclusion
- Dyeing in a machine gives a more consistent result.
- Dyeing by hand preserves the quality of the rope.
- Dyeing rope in full rolls is costly and hence very rare.
2. Dyeing rope
If you would like to dye ropes yourself, certain aspects should be considered. We will address the following points in-depth and give you useful information for dyeing rope.
- Choose material
- Choose type of color
- Dyeing process
- Drying
2.1. Material to be dyed
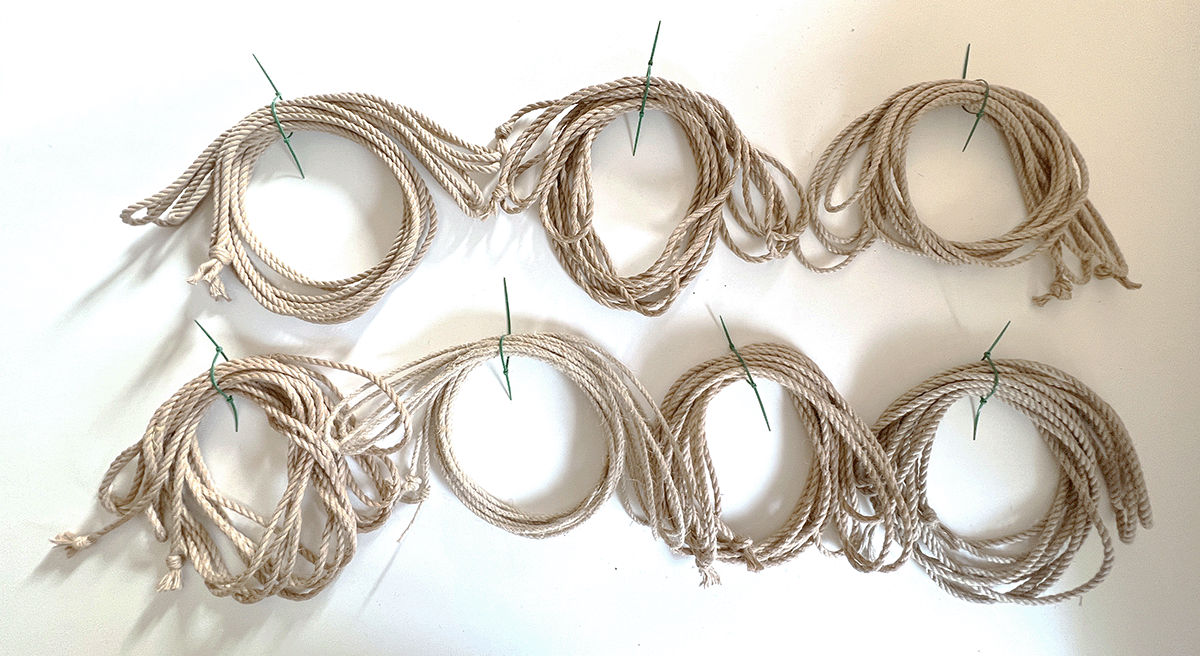
Different materials are suited better or worse for dyeing. Not suited for dyeing are materials like POSH, as they will not take any of the color particles into them. Furthermore, Jute is harder to dye than hemp or linen hemp. Linen hemp is well suited for dyeing, but hemp is the clear winner.
Comparison when wet
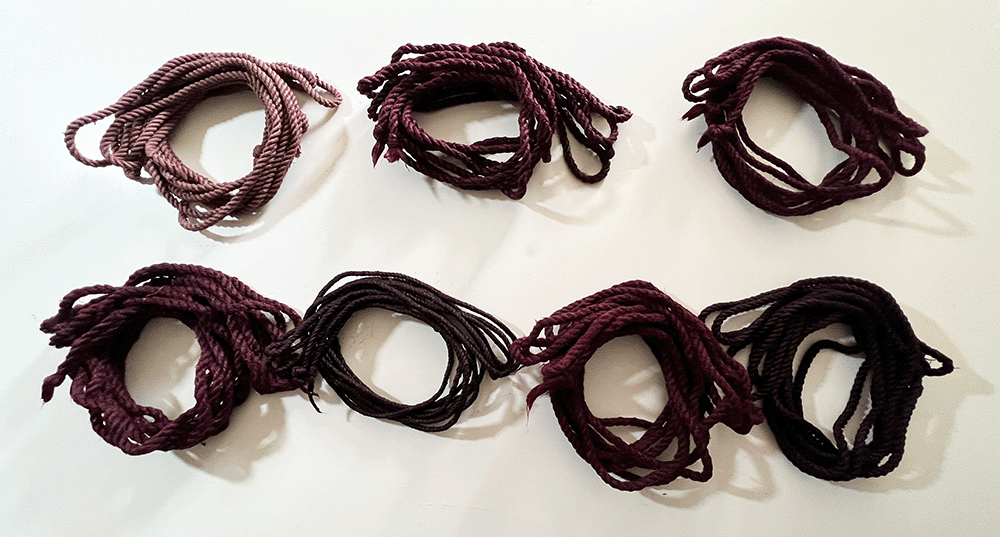
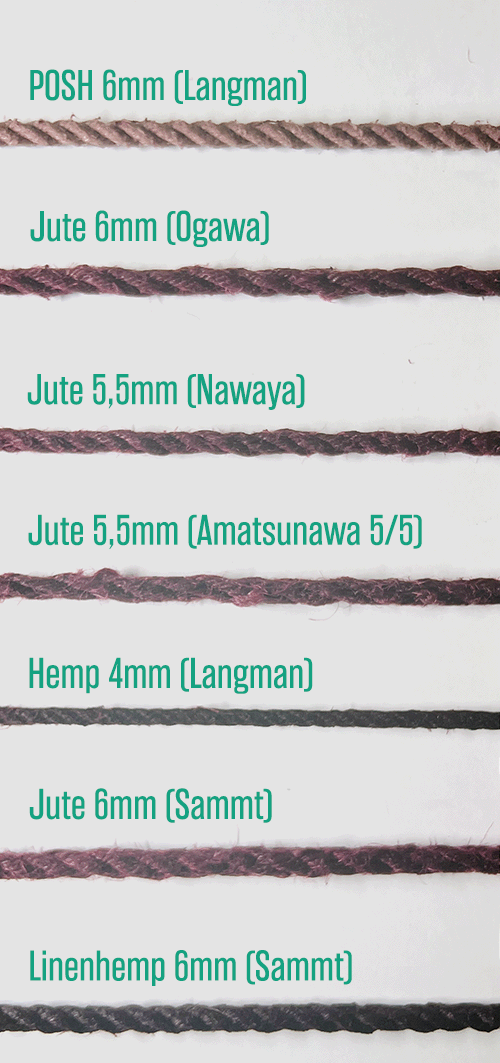
Result right after dyeing
As the comparison shows for the ropes in wet condition, the color difference is pretty obvious.
POSH can not be dyed at all, while hemp and linen hemp have the darkest (best) color. However quality of the rope is pretty much unchanged, which is expected, as it is ment for the rough sea and hence should be very durable.
Jute in general can be dyed, however only recommended by us, when using a suited product. Both loosely/loose layed ropes used in this experiment (Ogawa and especially Amatsunawa) show significant damage from dyeing in a machine. When dyeing by hand, this might not be a problem, however, looser ropes are more prone to loosing tension or being damanged when getting wet.
Linen hemp shows a very dark and nice color and only a few tension problems.
Hemp shows by far the best results in both quality of the rope, i.e. not loosing too much tension and intensity of the color.
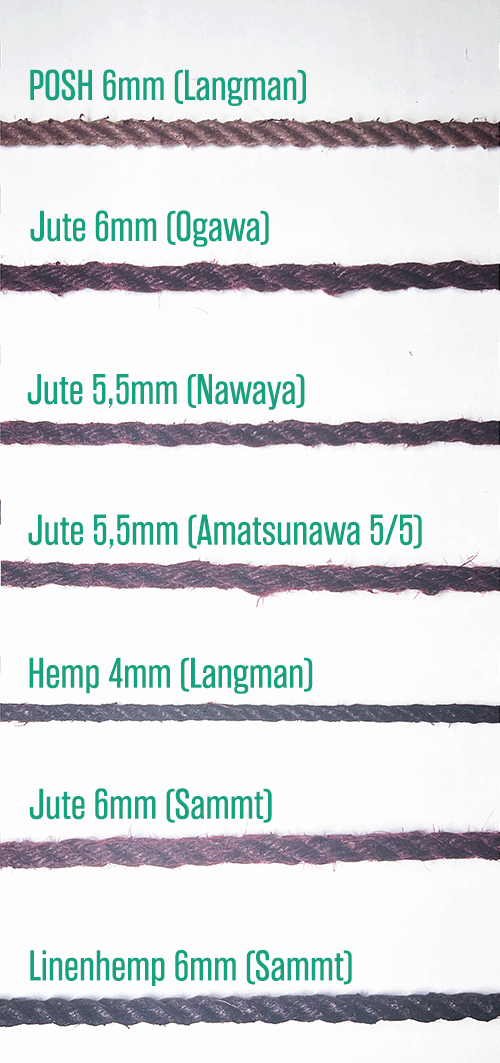
Result after one day
After 24 hours the ropes similar but the difference between hemp and jute is much more visible.
Dry, untreated rope after 1 week
Experiment is still in progress.
Finished and treated rope
Experiment is still in progress.
Differences for Jute
Even for the same material, there are huge differences. The rope, especially if it contains JBO and how it's layed needs to be considered. Loosely layed or ropes with JBO is less suited for dyeing. In terms of JBO, the ropes should be baked, to get rid of JBO in the rope, to allow color to penetrate the rope fibers. Loosely layed ropes, however, will easily get damanged if not careful. Hence loosely layed ropes should not be dyed in a machine.
Conclusion
2.2. Type of color
We are using simplicol products to dye our ropes.
2.3. Machine or dyeing by hand
Washing or making rope wet is a controversial topic itself. Therefore each step has to be considered carefully to stress and weaken the rope the least.
General differences
A washing machine has the benefits of continious movement. Hence, the overall dyeing is a lot more consistent when dyeing by hand. The amount of rotary movement, however, also has its drawbacks. In comparison to the results above, where the focus was on the materials and the differences in color, this time we wanted to stress the rope the least. It is very clear to see that the washing machine adds a lot of twist to the ropes itself. There are two reasons for it: 1) the rotation of the machine itself and the ropes turning inside of it and 2) the method of bundling your rope.
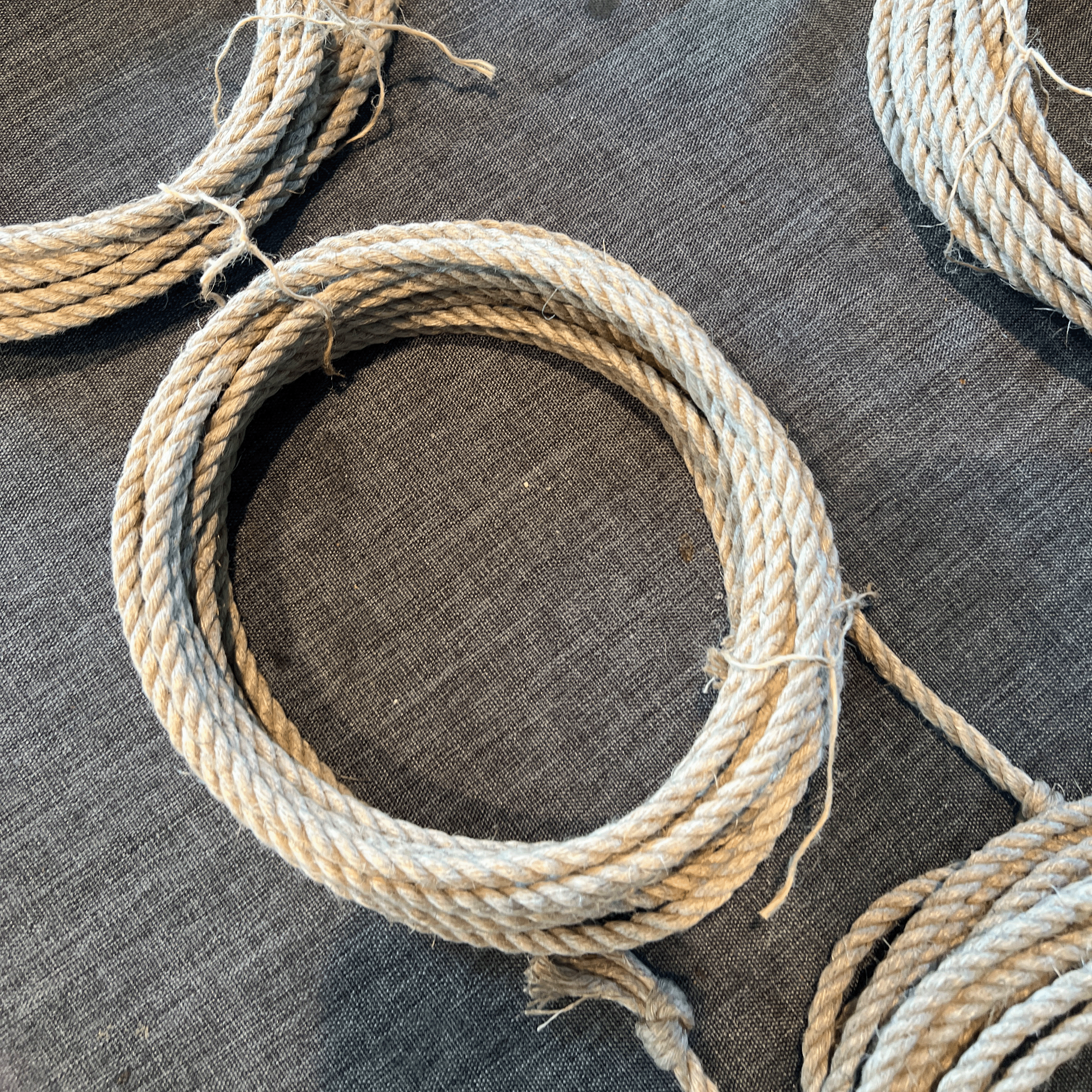
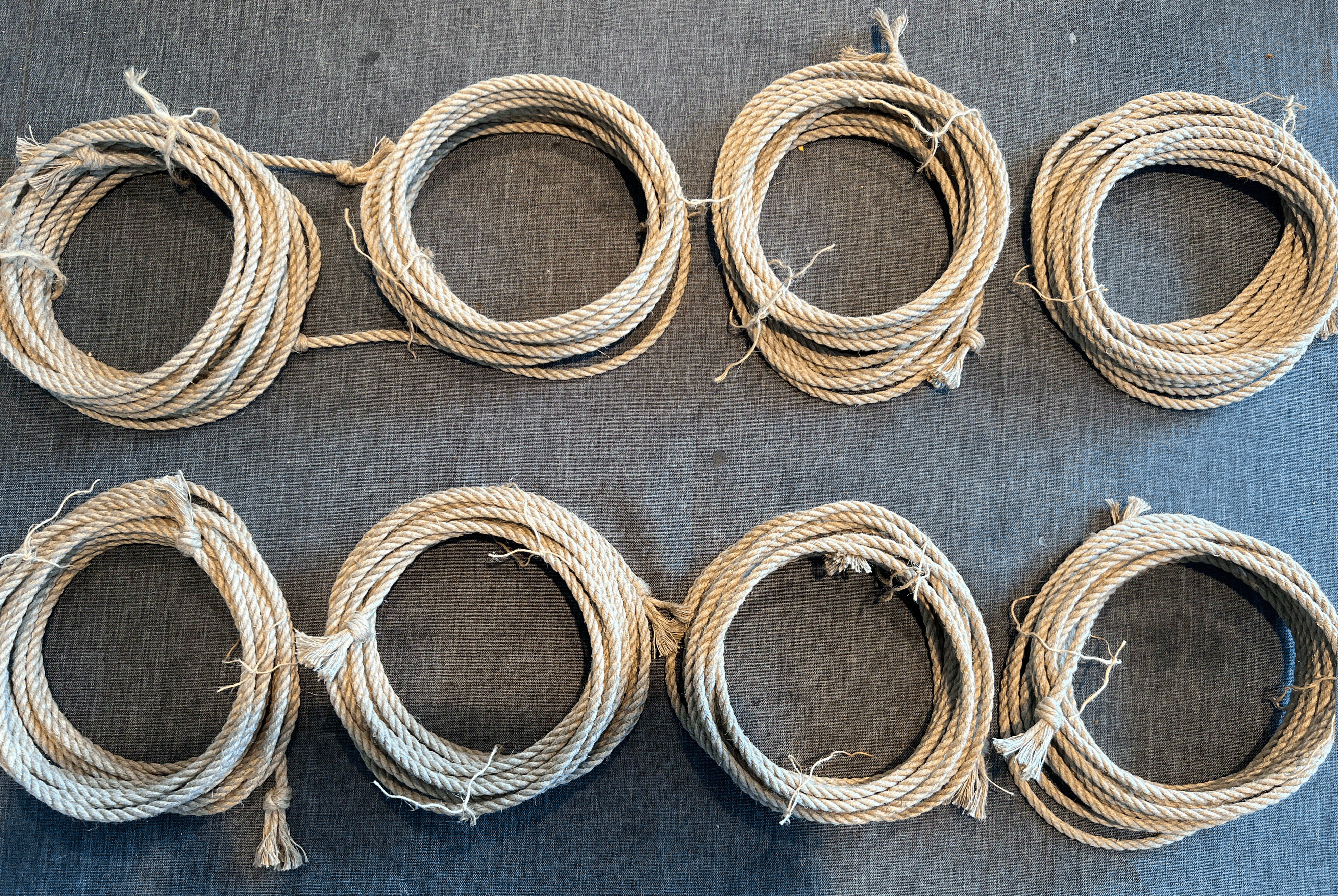
Rope bundles
As for treatment in the dryer, the method of laying the rope into bundles is very important. Any additional turn or twist will stress and weaken the rope additionally. Therefore it is extremely important to lay ropes evenly. We are using a blackroll to bundle the ropes by turning the roll and wind up the rope in a tight manner. Afterwards we secure the bundle with two yarns of rope on two opposite sides.

Preparation, Process and Parameters
In the first try, we have stuck to the recommendation of 6 liters and 1 package of color for 300g of material for dyeing. Hence, we used 18 liters of water and 3 packages. The result, however, was not perfect and the ropes were not fully dyed to the inside. We are now using 5-7 liters of water and three packages of simplicol expert color for 1.3kg of material. The water is heated to 60°C and the color is added and mixed well with a wooden stick. Once well mixed, we add the rope to it.
During the process, we keep the temperature at 60°C and mix the ropes a bit every 15 minutes for at least 2 hours. Afterwards, the heating is turned off and we release the water at around 40°C and clean the rope with cold fresh water.
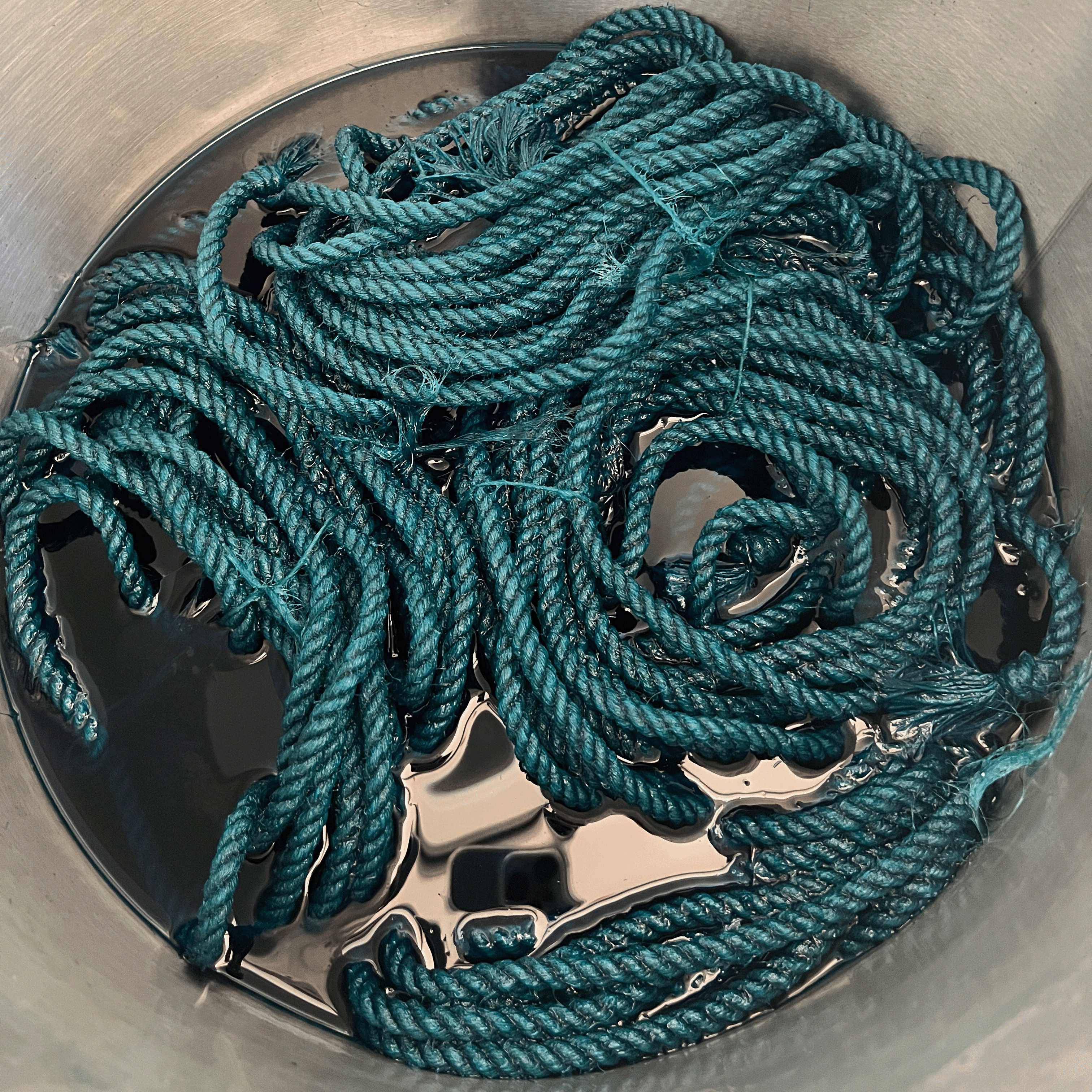
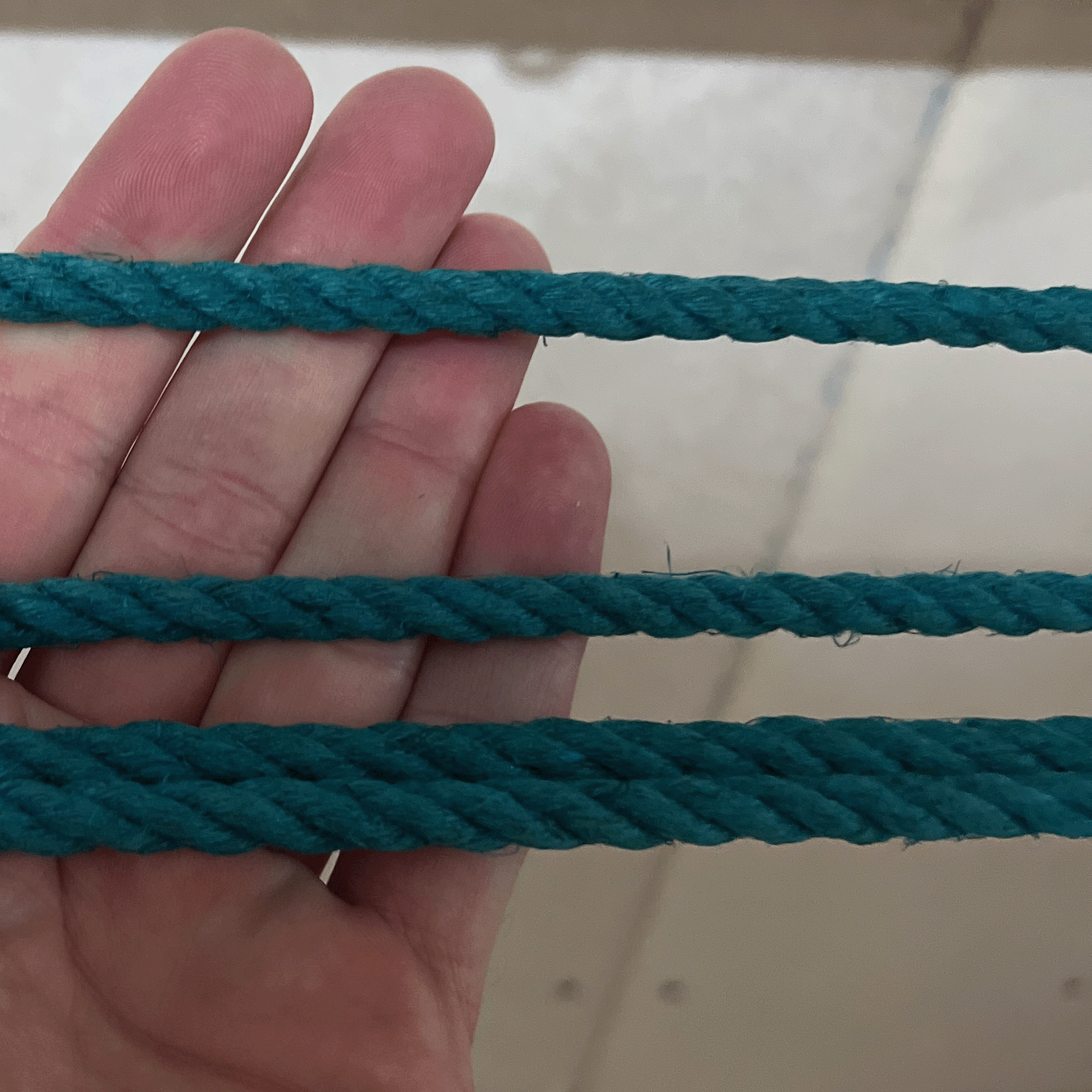
2.4. Drying
Drying should be slow, to give a better result for the rope. This means don't put your rope into your dryer right after dyeing. Furthermore, dyeing should only be performced under tension of each rope. As a rule of thumb 1kg per meter should be applied to the rope during horizontal dryeing. In addition, using the older techniques to wrap rope around two or more rolls that are under tension can be successful but is not recommended, as tension might be way too low. We use a method, where each individual rope end is attached to a weight or rubber band for applying the weight or force to the rope in full length. This allows the rope to dye evenly and slowly.